The 5-Step Breathing Air Purification Process
Breathing Air Requirements and Regulations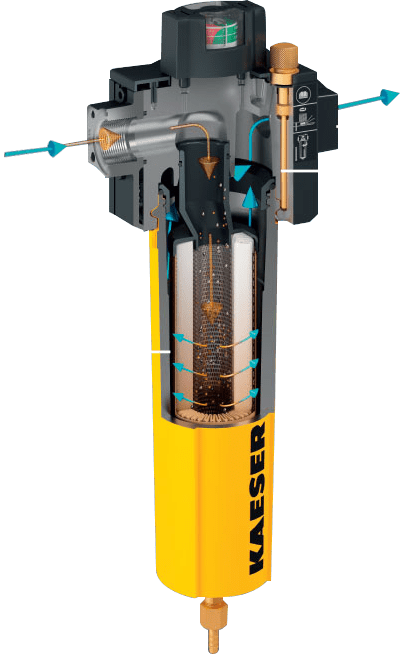
Since the Clean Air Act of 1970, CSA and the Occupational Safety and Health Administration (OSHA) have set air quality guidelines to protect workers in a variety of industries. Certain sectors with unique risk factors, such as chemical exposure, may need to follow stricter regulations. Many commercial and industrial systems include surveillance alarms, like carbon monoxide detectors, and purification devices.
These guidelines all have one goal: To ensure consistent, reliable breathing air quality.
Common Compressed Air Contaminants
Some of the most common contaminants of ambient air include:
- Oil
- Water vapor
- Carbon monoxide
- Dirt
The breathing air purification process is designed to remove common air contaminants. To circulate pure air throughout the structure, multiple air compressors must be positioned around the area.
The Five Step Purification Process
The process of purifying breathing air consists of five major steps.
1. Removing Liquid Oil
An air compressor can remove oil droplets as small as 0.01 parts-per-million (ppm). During this process, compressed air flows through a blended-fiber coalescing filter.
2. Removing Water Vapor and Liquid 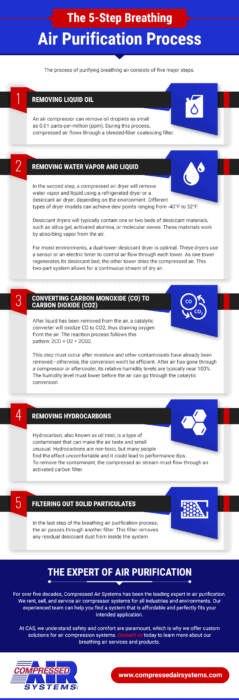
In the second step, a compressed air dryer will remove water vapor and liquid using a refrigerated dryer or a desiccant air dryer, depending on the environment. Different types of dryer models can achieve dew points ranging from -40°F to 32°F.
Desiccant dryers will typically contain one or two beds of desiccant materials, such as silica gel, activated alumina, or molecular sieves. These materials work by absorbing vapor from the air.
For moist environments, a dual-tower desiccant dryer is optimal. These dryers use a sensor or an electric timer to control air flow through each tower. As one tower regenerates its desiccant bed, the other tower dries the compressed air. This two-part system allows for a continuous stream of dry air.
3. Converting Carbon Monoxide (CO) to Carbon Dioxide (CO2)
After liquid has been removed from the air, a catalytic converter will oxidize CO to CO2, thus drawing oxygen from the air. The reaction process follows this pattern: 2CO + O2 = 2CO2.
This step must occur after moisture and other contaminants have already been removed—otherwise, the conversion won’t be efficient. After air has gone through a compressor or aftercooler, its relative humidity levels are typically near 100%. The humidity level must lower before the air can go through the catalytic conversion.
4. Removing Hydrocarbons
Hydrocarbon, also known as oil mist, is a type of contaminant that can make the air taste and smell unusual. Hydrocarbons are non-toxic, but many people find the effect uncomfortable and it could lead to performance dips. To remove the contaminant, the compressed air stream must flow through an activated carbon filter.
5. Filtering Out Solid Particulates
In the last step of the breathing air purification process, the air passes through another filter. This filter removes any residual desiccant dust from inside the system.
The Expert of Air Purification
For over five decades, Compressed Air Systems has been the leading expert in air purification. We rent, sell, and service air compressor systems for all industries and environments. Our experienced team can help you find a system that is affordable and perfectly fits your intended application.
At CAS, we understand safety and comfort are paramount, which is why we offer custom solutions for air compression systems. Contact us today to learn more about our breathing air services and products.